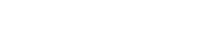
How-to Cast Pewter
Clip: Season 3 Episode 6 | 6m 50sVideo has Closed Captions
How-to Cast Pewter @ Hammerspace Community Workshop
David Dalton instructs our host, Matt Burchett, on casting pewter challenge coins.
Making is a local public television program presented by KMOS
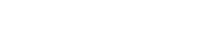
How-to Cast Pewter
Clip: Season 3 Episode 6 | 6m 50sVideo has Closed Captions
David Dalton instructs our host, Matt Burchett, on casting pewter challenge coins.
How to Watch Making
Making is available to stream on pbs.org and the free PBS App, available on iPhone, Apple TV, Android TV, Android smartphones, Amazon Fire TV, Amazon Fire Tablet, Roku, Samsung Smart TV, and Vizio.
- [Matt] Now are you taking that flash off with that wheel also?
- [Dave] Yep.
- So we're back here today at Hammerspace and I'm standing here with Dave and you've got quite a bit of stuff laid out for us here.
What sort of project are we working on?
- Well today, you're in luck.
We're gonna be doing a really fun project where we're gonna be casting some metal.
Now metal casting is generally fraught with all sorts of peril, special equipment, super high temperatures.
- Yeah, we're not wearing respirators here.
- No, it's nothing like that.
It's pretty tame for metal casting.
I think metal casting is really like the foundational element of all of the metal arts because before we could do anything else, we needed to cast some metal into a single piece so we can use it for, - I have to make a tool so I can make my other tool that I need.
- Exactly.
So from that first campfire where some shiny metal coagulated under the campfire, humanity's been casting metal.
Now the bronze age is named for bronze, which is an alloy of copper and tin.
- [Matt] Okay.
- And it's really hard to melt bronze in your house.
Like you need about 2,000 degrees to melt bronze and that's hard to achieve in normal circumstances and without special equipment.
- And air conditioning space and all that.
- Exactly.
So today we're gonna use anti bronze, kind of the opposite of bronze if you will.
- Okay.
- It's pewter.
- All right.
- Now pewter's a different alloy with exactly the same stuff in it.
It's also made out of copper and tin, just in opposite ratios.
- So far more tin than copper?
- Almost all tin with a little tiny copper as opposed to being almost entirely copper with a little bit of tin.
Paper burns at about 451 degrees Fahrenheit ish.
And MDF or medium density fiberboard, is considerably thicker than paper.
So this is just the same stuff that paper's made out of.
This is sawdust reconstituted into a solid piece of material and this is durable enough to withstand molten pewter being poured onto it.
So today we've made something called a billet mold.
This is an entirely digital process.
We drew these on our computers, over in the computer lab, using a vector drawing program.
So just graphic design software, and we drew some logos and laid them out and then took that design down to the laser shop.
Over in the laser shop we used some CO2 lasers to cut and etch these into the final shape.
- So that was all one process and one machine?
- Yes, one machine did the etching and the cutting all at once.
This helps us with registration.
Now this part of it, we have sort of this channel that comes down to our coin shape at the bottom.
And this is replacing structures in a regular casting process known as the button, which is kind of the fill spout of our mold and the sprews, which are straw like appendages that go to different parts of your part to help deliver metal to those parts and to evacuate air from the part.
- [Matt] Well, what's our first step here?
- Well our first step is to take some of these shapes and assemble them together.
So if you'd like to pick out something, I've got a couple here that I've already pre-built.
- Let's go.
We'll do my logo and your logo there.
- [Dave] All right.
So go ahead and stack those up.
- [Matt] Okay.
- I like to make sure that it's nice and flat on a table or surface when I start.
And we just wanna put some pressure around the perimeter so it doesn't leak.
And then I usually use these to get it a little stability there.
Make a little stand out of our clamps, and then we'll want some safety glasses because if we should splash some pewter, it should just roll off of us, but not our eyes.
- [Matt] That's fair.
- So then we'll take some of our clean pewter and we're gonna pour it into our mold.
We want to kind of pour it all at once so that we fill all the way up to the top and a little over spill is just fine.
- [Matt] Now how long will that need to sit in the mold until it's ready to come out?
- [Dave] Only a minute or two.
- Okay.
Because it's not, there's not a whole lot of mass there.
- It's pretty thin.
It's gonna be hot for probably about three or four minutes and then it should be ready to demold at that point.
- Okay.
Okay, so it's been, we've had that in there for what, three or four minutes, give or take?
- [Dave] Yeah, more or less, three or four minutes and now we can see what we've got.
There we go, it's cool.
Now at this point it's gonna be hard to see the details because we're gonna have all sorts of surface discoloration from the casting process, but, - [Matt] That didn't turn out bad at all.
- And that's our first try on this mold.
Now typically your second casting on a mold, looks a little better than your first one because MDF is full of glue and formaldehyde and all kinds of other stuff that boils just a little bit at these temperatures so it'll mess up our surface finish.
- [Matt] So you kind of like caramelized the mold?
- The surface.
Right, right and now the second casting in it, it's like going into a carbon mold now, it's gonna do much better on a second casting.
And then I've got some shears here that we can separate our excess material and so it wasn't wasted, even though we poured all that extra material, it just goes right back into the caster and gets recycled.
- Perfect.
- So now that we've cleaned up the edges of our coins a little bit, got rid of the remnants of the sprew and, - We're just talking about the little, - Just that little bit that's left there.
I cleaned that off of this one and it's all ready to go.
But they look a bit humble when they come out of the mold because we just have the raw surface of the metal there.
So I have a secret that I use for patinaing these coins.
It's a dry erase marker because we want to use something that's really permanent.
- [Matt] Perfect.
- And then we're gonna wipe it off with some steel wool.
Now this is not ordinary kitchen steel wool.
This is some for fine finishing.
It's like a quadruple OT steel wool.
So the type with the four zeros on it, this is really, really fine.
- [Matt] Right.
- [Dave] So this isn't gonna scratch our coin up, it's just gonna shine it up and give it a little luster.
- [Matt] So you said we can reuse these molds.
We've got a couple more molds to use and we've still got some metal hot, what do you say we make a couple more?
- [Dave] Let's make a pile of coins.
- [Matt] Let's do it.
So that didn't take very long at all.
We got a pile of coins going.
- Yeah, I feel like we will just open our own mint right here and start minting our own currency.
Hammerspace Community Workshop
Video has Closed Captions
Hammerspace Community Workshop – Kansas City, MO (6m 21s)
Video has Closed Captions
Hannah Klein Design – Pressed Flowers – Neosho, MO (5m 35s)
Making is a local public television program presented by KMOS