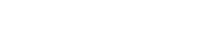
Making #205
Season 2 Episode 5 | 26m 47sVideo has Closed Captions
MO School of Blacksmithing, Barb Byrne: Glass Artist, Pat Berkbigler: Gourd Artist
On this episode of Making we: forge relationships and hard hitting skills at this traditional trade school, mold molten glass to fit any occasion, and turn hard shelled fruit into delicate artwork…
Problems with Closed Captions? Closed Captioning Feedback
Problems with Closed Captions? Closed Captioning Feedback
Making is a local public television program presented by KMOS
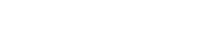
Making #205
Season 2 Episode 5 | 26m 47sVideo has Closed Captions
On this episode of Making we: forge relationships and hard hitting skills at this traditional trade school, mold molten glass to fit any occasion, and turn hard shelled fruit into delicate artwork…
Problems with Closed Captions? Closed Captioning Feedback
How to Watch Making
Making is available to stream on pbs.org and the free PBS App, available on iPhone, Apple TV, Android TV, Android smartphones, Amazon Fire TV, Amazon Fire Tablet, Roku, Samsung Smart TV, and Vizio.
Providing Support for PBS.org
Learn Moreabout PBS online sponsorship- [Matt] On this episode of Making, we forge relationships and hard-hitting skills at this traditional trade school, mold molten glass to fit any occasion and turn hard shelled fruit into delicate artwork.
That's all next, here on Making.
This program was made possible by contributions to your PBS station from viewers like you.
Thank you.
(slow folksy music) Hello, and welcome to Making, the show dedicated to makers and the artistry of their craft.
I'm your host Matt Burchett.
Thank you so much for joining us.
This week, we begin here with a very hot hands-on learning experience at the Missouri School of Blacksmithing.
A little later on in the show, we'll catch up with the master craftsman himself to help me hone some of my own tool making abilities.
But first, we look in on a class of aspiring forgers, made up of fathers and sons, working hard to ensure that these old world skills carry on to the next generation.
- [Matthew] I opened the Missouri School of Blacksmithing in 2016.
There had not been a blacksmithing school in Missouri, or for that matter, the Midwest, for several years.
There was a definite need for quality instruction on blacksmithing, someplace where people could come and do a intensive, hands-on class learning the basics of blacksmithing.
I already had been doing blacksmithing for several years and I had done some teaching just one on one with people and found that I had a natural talent for it, I guess, where I was able to explain things, I guess, in a way that made sense to people, that worked well with people and break things down into manageable pieces.
So when I'm teaching a class, I talk about the basic equipment of blacksmithing, the forge, the anvil, hammers and tongs, and like the different parts of the anvil.
The heel, the horn, the hardie hole, the pritchel hole.
So students know what I'm talking about whenever I'm doing my demonstration and instructing them.
We cover six of the seven basic forging operations.
Drawing out, making a bar smaller and longer.
Upsetting, basically hammering it in the opposite direction to get more material on the end of a bar in a particular area.
Twisting, doing decorative twists, functional twists.
Bending, bending a hook, bending a 90 degree corner or whatever.
Cutting, cutting a bar in half, making two times for a chisel or something, cutting it off.
Punching.
And then forge welding.
One of the first things we do is light the forge, get it going.
We use coal forges.
And getting a piece of steel hot.
And then we just take a round bar and we work on hammering it square.
So, that's what I tell 'em.
"We're just kind of getting warmed up.
We're learning how the forge keeps up steel."
If they need to make adjustments to it, move it back and forth to get different areas hot, we can do that.
And then just getting used to hammering, you know?
It kind of takes some coordination and some practice to get used to doing that.
Then we move on to more advanced things.
So we go from squaring up that bar to drawing out a bar.
So squaring it up and then working it down to a taper.
And then that taper, that square taper, we hammer into an octagon and then a round shape, and then curl the end and bend it around for a wall hook.
And then we put a twist in the bar, and then on later projects, we'll flatten a section and punch a hole in it.
And I show 'em how to make a nail and we make a nail that will fit in the hole to hold up their hook on the wall.
So it's progressive, moving from simple things to increasingly complicated things, adding those basic forging operations in there as we go.
So it's working right on the edge of their abilities where they're challenged with it, but they're not working in over their head where they're gonna get frustrated either.
- [Luke] We're making a leaf shape and it's really hard.
It's hard, yeah.
My favorite part has been seeing how the things that I'm making turn out.
- And beating your dad.
Yours looks a lot better than your dad's don't they?
- Yes, they do.
(Dan laughs) - [Dan] I think just understanding the basics of just the skills and the trades out there is useful for our next generation, right?
We just go to the store and buy everything.
So understanding how things are made and that there's all kinds of different ways to get things done.
And... Luke is really interested in doing stuff with his hands.
And I just thought it would be something we could share together.
We do some neat stuff around our small homestead and, you know, I thought maybe some of these skills might transfer to some of our needs there.
I just think there's just a lot of opportunity for Luke to learn some different skills and trades that he might be interested in long term.
- [Matthew] What I emphasize with the school is being able to do things hands on really works well.
That there's a value to that, that people that aren't doing it hands on may not instantly recognize.
But once the students come, I demonstrate how to do a particular project.
Actually go to their forge and anvil and work on it.
It really clicks for them.
It really connects.
And that's really, I think, a valuable, probably the most valuable way to learn.
So I've tried to create the best environment I could for people learning, in a intensive environment, a three-day class so that they're really getting the best foundation they can in order to progress with it or really learn what it's about.
- [Barb] I started in the arts probably when I was in high school.
After I got married, I started doing upholstery, I was plastering furniture, and then moved into other fiber crafts.
We lived on a farm in the middle of Missouri, 300 acres.
And I joined a group that did sheep shearing and those kinds of things.
And I got into wool and I did some felting and then some basket weaving.
But basket weaving was really the one that hooked up for me.
So for a lot of years, I was a basket weaver.
And then I started growing gourds and got into gourd craft.
I married the basketry and the gourds with weaving.
So I would weave the tops of gourds with ornate types of rims.
Found that there was a class at a community center here in fused glass.
And I had always been interested in glass, so I thought, let me check out this fused glass thing.
So I did that for about six months.
I knew I was hooked on glass and I loved that.
And then I guess about six years ago, I met a woman who was doing what's called powder painting.
And what that is, powders are crushed glass and they come in various sizes.
So there's three or four different sizes of, it's called frit, is crushed glass.
They're three or four sizes of frit, and the smallest size is powder and it is like powder.
And so she was sifting powder onto glass pieces and actually making images.
She wanted to do a tutorial on how to do kitties.
So I partnered with her and I, she did the tutorial and I tested it for her.
So I made my first glass kitty using her tutorial and absolutely fell in love.
Almost all of my pieces are two layers of glass.
I start with clear glass that has nothing on it.
I choose the image that I wanna reproduce and then I determine what part of that image goes on the back piece of glass and what part of the image goes on the front piece of glass.
And then I work on those separately.
So then after I've got both sheets of glass the way I like them then I have to fire them together.
And that takes what's called a full fuse firing, which means I have to take it up to like 1,465 degrees to get those two pieces to melt together.
My husband and I, over the last couple of years, my husband is also an artist and he does found art.
He likes to create things from found objects.
So over the last couple of years, we have collaborated on some pieces.
For example, he had a piece that was accepted into the St. Joe Sculpture Walk last year.
And it was a tall piece of wood and metal that he made and he drilled holes in the piece.
And I made glass butterflies that we put in all of the holes.
So that's one of our collaborations.
Becoming a juried artist is probably one of the goals that I set for myself.
Becoming a juried artist means that you put your art out there for the art community to look at.
And in the organization, every organization has a jury committee and they look at the art and they assess it for content and composition and art knowledge.
And they give it a designation that kind of moves you up into the art world and makes you a, quote, "fine artist."
So it was important to me to become a juried artist because so few glass people are juried into organizations because frankly, a lot of the art world doesn't understand the glass process.
And so it's not viewed necessarily as a fine art.
I think the most exciting thing about doing glass is putting something in the kiln and not knowing what it's gonna look like when you open up the kiln.
I have been very fortunate in that, most of the time, most of the time, when I open the kiln, it's a pleasant surprise.
A lot of the time it looks way better than I ever thought it was going to look.
And for me, if I can run my kiln almost every day, I let it run during the day and then it has to cool down to room temperature overnight.
So I fire during the day most of the time, let it cool overnight.
So every morning when I get up, the first thing I do is come up to the studio and open the kiln.
And it's like Christmas morning every morning of my life when I'm using the kiln.
- So we're back here at the Missouri School of Blacksmithing and I'm standing here with Matthew Burnett and he's gonna show us how to make a better set of tongs than I've been able to make in the past.
So back in 2014 when I first started forging, I decided I was gonna make all of my own tools too because you know, it's just, as a blacksmith, you want to be able to make all the stuff you need.
So I set out to make myself a set of tongs and I failed pretty handily, and I've kept them all this time because, you know, you gotta remind yourself where you came from.
- Yes, that's right, yeah.
- But since I failed so badly at them, I felt, I've switched to using laser-cut tong blanks for any tongs that I've made in the past, which is something like this.
So you get kind of the blank and you do a little bit of forging, you twist the jaws, you rivet 'em together and you're done.
So it's expeditious but it's cheating.
- Yeah, it kind of is cheating, yeah.
That's what I tell people, you can do that and everything, but you're not really learning how to make tongs like that from just a bar of steel.
So I'll show you what we're gonna do here.
We're gonna start off with a piece of 5/8th round.
This is seven inches long and I've got two of these already cut the same length.
So we're starting off with one bar for each side of the pair of tongs.
And that's about what it's gonna look like whenever we're done.
So we'll forge out the jaw, the boss area here where the rivet is, where they pivot and everything.
And then the reins, the handles.
And we'll size them to whatever size steel you want.
You can make 'em for even the same size that you make the tongs out of, 5/8th's or whatever.
And I make these all with a V bit here so that they will hold both round bar and square bar.
So yeah, we can go ahead and take a heat on this and I'll show you what we're gonna do.
Heating up the bar field and I've got a mark there on the anvil.
How long I want that jaw.
So I can do both sides the same.
That's important that we get both sides to match.
- [Matt] So we're just forging in transitions at this point.
- [Matthew] Transitions, yeah.
We're going from a round bar into the jaw and boss and everything.
So it's gonna start to look like a pair of tongs here.
So I'm keeping the bar pressed down on the anvil as I do this, make sure it's not gonna bounce around on me.
And of course it's gonna get drawn out a little bit.
It's gonna be a little bit beyond that line by the time I get done here.
So I started off like this, and do a quarter turn to the left, and I'm gonna come up here about 30, 45 degrees over the edge of the anvil where it's still around here, just drive it down here, again, keeping it pressed down in place where it's not gonna bounce around on me.
I'm gonna do another quarter turn to the left, come up roughly a square-ish section and drive it down again.
We've gotta do that beginning of the handles, the reins and the back part of the boss here.
- [Matt] So then you've got- If you look at it, you can see the very beginnings 'cause you've got your tong jaw.
You've got the boss and then you've got where your handle, or your rein's, gonna start.
So you're just starting to try and thin out and define those different area.
- Yeah, that's right, yeah.
And I wasn't trying to do all of that at once, in one heat or anything.
I'm gonna cycle back through that several times in order to develop this shape to get that jaw nice and square here to get that boss area widened out and everything.
And then start drawing this section down here that's gonna become the reins.
And I'm just doing one half right now.
But usually what I do on these is go ahead and work on both sides at the same time.
That way I'm just following them in rapid succession.
I find it's a lot easier to make both sides match like that.
So I flip the tongs around here, gonna grab a hold of the jaw with another pair here, got a good grip on 'em and everything.
Come over here to the power hammer and start drawing out these reins.
So our next step here is to punch the hole for our rivet where both of these halves of the tongs are gonna be riveted together and pivot here.
So just gonna eyeball that there in the middle of my boss area.
Keep that punch pressed down.
And there I've got my hole and then there's the little slug I punched out.
And you can see I've got a nice clean hole.
And make sure it fits our rivet here.
We need to drift it open a little bit, need to stretch that a little bit bigger.
So we'll just drive our punch in there a little bit more.
And we're just gonna put a mark down through the middle of this jaw to mark the center that we're gonna bend for a V to go around our bar of steel.
So this is gonna be made to hold a square bar, but if we make it right, it'll hold both square and round in that same site.
And then the next step here, 'cause I'll get this hot, and we'll go over here to this V-block in the power hammer.
So I've got a V on the bottom and then a V on the top here, put it down in here, get this all lined up the way I want and come down on the power hammer with it and bend that flat section into a V here.
And then we can just refine that just a touch.
I'm gonna bend this down just a little bit.
So we've got our boss forward.
I'm gonna bend the jaws down just a little bit, I'm dropping my left hand as I do that.
Okay, wanna make sure we're flat on that boss.
Our rivet should still fit.
Yeah, that looks good.
- I'm gonna try and repeat what Matt's done here.
(intense country music) - Okay, I'll go ahead and go with this.
And this is where it's nice having two people.
Okay, let's look at it there.
Hey, it looks like we estimated the right amount of material.
Got a completed pair of tongs there, did a pretty good job on that.
You were able to match your side to my side and look good.
Got your touch marks on there and everything so it should be a good tool for you to use.
- That's pretty awesome.
Well, I had somebody helping me all along the way.
I'm sure I could have made way worse work of it if I hadn't had somebody here with me.
Thank you so much for letting us come and see your shop and helping me out with these.
This has been great.
- Well you're very welcome.
- Appreciate it.
- Thank you for coming.
- [Pat] I was an elementary teacher for 31 years but didn't have anything to do with art.
I never took an art class or taught art or anything 'cause everybody always asks me that.
But I just have dabbled in crafts and so forth my whole life.
So I was looking on YouTube to find some ideas and came across Miriam Joy's gourd art.
And she had Coyote gourds, which is a small round gourd that you collect out of the ditches, and then you green peel them and she made them into ornaments by painting them and then using melted crayon.
And I was like, "Oh well that's cool, I'm gonna try that."
So I ordered my stuff and got going and then decided I'd like to try it on some larger gourds but I didn't have a clue where to get them.
And then came across the Show Me Gourd Society who has a gourd festival every year in Springfield.
So I took a class there in carving and that was it.
I was hooked.
The process of doing gourd art from start to finish is you'll get a gourd.
And you can get them two different ways.
You can get them unclean.
And so this one is covered with mold and all that mold has got to come off.
But you can get them clean too.
You pay more for the ones, of course, that are clean than the ones that aren't.
So it depends on what you wanna do there.
But if you get it covered with mold, then you need to soak it.
I put it in a tub and put a wet towel over it and soak it for a couple hours and then use a steel scrubbie.
So then once I've used the steel scrubbie to get all the mold off, then it looks like this.
And so that's a clean gourd, and then you have to open it up and get all the seeds out.
And so it's filled with seeds and it's like a papery substance inside and it's all attached to the walls.
I use cleaner balls that I attached to the end of a drill and I can put those cleaner balls in there and drill around and get all that stuff out.
And that all needs to come out because if you don't take it all out, eventually it's going to come out.
So if you paint the inside, it'll peel off later if you don't get it good and clean at the beginning.
So you get it good and clean, and then I put my design on there.
And usually I draw it on another piece of paper and then transfer it with graphite paper onto my gourd.
Once I get the design on there, then I use my pen, my pyrography pen, and outline everything, woodburn everything.
And then after I woodburned it all, then I paint it.
And then after I paint it, that's when I remove the background and, it's called stripping the surface of the gourd, before I do any carving.
So that's a painted gourd, but the next one over is just a carved gourd.
So on that one, I just draw it on with pencil and then start carving.
And once that's carved and everything, after you carve, then you sand, sand, sand, sand, sand.
Because once you paint that, any little dent... You might not see it, but once you paint it, you're gonna see it.
So you have to do a lot of sanding.
Once it's sanded, then you paint.
And then I spray it with an acrylic finish.
Several, two or three coats, of acrylic finish to preserve it.
When you're trying to do a gourd, the gourd can generally tell you what you can do with it.
So if you're going to do some deep carving, you need to have a a thick gourd.
And in order to have a thick gourd, you generally need to get it from California or Arizona.
There's a couple of gourd farms there, big operations, and they can grow them nice and thick.
Some of them I've gotten have been almost an inch thick.
In Missouri here, we can't grow thick gourds like that.
We just don't have the right weather.
Their growing season is hot and long and ours is not.
So the thinner gourds will come from Missouri and Kentucky, but those are fine too 'cause those are ones that I use for cutwork.
You really don't want a thick gourd when you're doing your cutwork.
Generally you can kind of feel the gourd and think, "Okay, this is gonna be a nice thick one."
But when you open it up it may not be at all what you thought.
And so once you clean the inside of it out and get all the insides in out, then you see just how thin it is.
So you may have to change what you thought you were going to do with that gourd.
So some of them I try to open up, and have several open, so that I can see what they are so I can know what to do with them.
So I get an idea in my mind and then I can go pick the gourd to do what I want to do.
And if you want to learn the different things you can do with gourds, then the best thing to do, to me, is take a gourd class.
'Cause you'll have somebody there who really knows what they're doing, which was very helpful to me.
And I've looked online and done things online too, but I've always find that if I take a class, I get way more out of it 'cause I'm actually doing it as they're teaching it to me.
So around the United States, there are a lot of gourd societies.
Almost every state will have a gourd society and they usually have a gourd festival every year.
And at those gourd festivals they teach classes.
And so, depending on what you want to learn, they generally have classes from very basic things to more extensive.
But usually every class has something for everyone.
Even if you've done it for a long time, the teacher will have some technique or something that you've never heard before or have never tried before.
I really like the carving.
Doing ripples and the filigree and the stippling and those kinds of things.
I like the carving part of it.
The paintings, like I say, I've never taken an art class or done any kind of art course.
So the painting is kind of nerve-wracking for me.
I enjoy, I mean, just keep working at it, working at it 'til I finally get it to look like what I want it to.
But I think if I was a painter, I could do that a lot faster than I do.
But that's okay too, 'cause it's just a whole different thing.
And whenever I'm carving or painting, whenever I'm working on my gourds, it just takes me away from everything.
I'm just in my zone and it takes away all the stress and anxiety that has come around lately.
And so it's a great release for me.
So it's very, very relaxing and very therapeutic.
- That's all the time we have for this week, but we hope all of our makers have inspired you to unlock your creative spirit.
We thank you all for watching and we hope you'll join us next time to see what we'll be making.
More information is available on social media or online at kmos.org.
This program was made possible by contributions to your PBS station from viewers like you.
Thank you.
(slow folksy music)
Video has Closed Captions
Clip: S2 Ep5 | 5m 41s | Barb Byrne, Fused Glass Artist – Pleasant Hill, MO (5m 41s)
Video has Closed Captions
Clip: S2 Ep5 | 5m 58s | Missouri School of Blacksmithing – Cameron. MO (5m 58s)
MO School of Blacksmithing How-To
Video has Closed Captions
Clip: S2 Ep5 | 7m 13s | Missouri School of Blacksmithing – Cameron, MO (7m 13s)
Video has Closed Captions
Clip: S2 Ep5 | 5m 44s | Pat Berkbigler, Gourd Artist – Fulton, MO (5m 44s)
Providing Support for PBS.org
Learn Moreabout PBS online sponsorshipSupport for PBS provided by:
Making is a local public television program presented by KMOS