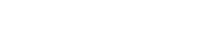
Making #306
Season 3 Episode 6 | 26m 47sVideo has Closed Captions
Hammerspace Community Workshop, The Tawny Canvas Calligraphy, Hannah Klein Pressed Flowers
Hammerspace Community Workshop offers tools, classes, and community to a variety of creators. The Tawny Canvas offers clients custom calligraphy and personal instruction through regular workshops. How-to Cast Pewter @ Hammerspace Community Workshop – David Dalton instructs Matt on casting pewter challenge coins. Hannah Klein Designs preserves flowers and memories using pressed flower art.
Making is a local public television program presented by KMOS
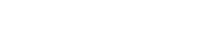
Making #306
Season 3 Episode 6 | 26m 47sVideo has Closed Captions
Hammerspace Community Workshop offers tools, classes, and community to a variety of creators. The Tawny Canvas offers clients custom calligraphy and personal instruction through regular workshops. How-to Cast Pewter @ Hammerspace Community Workshop – David Dalton instructs Matt on casting pewter challenge coins. Hannah Klein Designs preserves flowers and memories using pressed flower art.
How to Watch Making
Making is available to stream on pbs.org and the free PBS App, available on iPhone, Apple TV, Android TV, Android smartphones, Amazon Fire TV, Amazon Fire Tablet, Roku, Samsung Smart TV, and Vizio.
Providing Support for PBS.org
Learn Moreabout PBS online sponsorship- On this episode of Making, we visit a community that nails it when it comes to exercising their creativity, cross all our T's and dot all our I's, when we take pen to paper and preserve memories that will never wilt.
This program was made possible by contributions to your PBS station from viewers like you.
Thank you.
(upbeat music) Hello and welcome to Making, a show dedicated to makers and the artistry of their craft.
I'm your host, Matt Burchett.
Thank you so much for joining us.
This week we begin here at Hammerspace Community Workshop.
This space is made up of some of Kansas City's most creative makers and provides them with the tools, training, and community to tackle almost any project they can envision.
- I like to think of a maker space as kind of an enabling system for people with severe Attention Deficit Disorder.
If you stumble from one creative venture to the next and about the time you reach mastery, you lose all interest in that particular artistic venture, then the maker space might be for you.
This is a way that you can learn something until you've gotten all the dopamine mind out of it you possibly can and then go learn something new the next day and not have to feel bad about leaving piles of unused craft equipment in your spare room.
Many years ago when I was a blacksmith, I suffered a tragic loss of our blacksmithing facility to fire.
And it meant that many of the creative outlets that kind of, made up my creative life, were not available to me.
And so I moved on, did other things for a while, and years down the road in a woodworking business, 2008, the economic collapse killed the manufacturing company that I was working for and again deprived me of a whole collection of useful tools that I could use to use the opposable thumbs to make awesome things with.
And I realized that this must be true for a lot of people, that they reach some stage in their life where they've developed skills that require some sort of physical infrastructure to apply.
Whether you need table saws or you know, a black smithy or welding equipment or just a big open table with good light to work.
You might be in a situation where you can't manage that.
You live in a small apartment or your neighbor's complain about your anvil in the backyard or that sort of thing.
And so there are this, there's this need for people to have a space to be creative in.
So at Hammerspace, we like to make it possible to do creativity without any boundaries.
So we have sewing labs and 3D printing labs, sculpture labs.
We have an electronics lab with world class soldering irons, oscilloscopes, multimeters, power supplies, all of that.
A wood shop with everything you could need from A to Zed, in woodworking table saws and router tables, to drill presses and radial arm saws, panel saws, planers, joiners, all of that.
And then we've got a metal shop, which is my personal domain where I like to work, and it's full of blacksmithing equipment and welders and grinders and machine tools of all varieties.
So if you can't make it at Hammerspace, you should probably hire somebody to do it for you.
I think you could best describe our members as a rogues gallery.
There are so many different types of creative people here.
I mean, we have people who are fascinated with titanium and build everything out of it.
We have former architects turned digital designers of complicated custom objects.
We have sculptors who work in steel and other sculptors that work in wood.
We have special effects and prosthetics, makeup artists and costumers and cosplayers and swordsmiths and everyone in between.
Classes are primarily our way to reach out to the general public and provide a set of skills that will let you get into a new craft like blacksmithing or silversmithing or woodworking, to get your foot in the door and learn the basic tools and sort of make and take for adult creative people.
It's nice to be able to have a starter project that you can anchor a few skills to, so that the next time that you go into the shop, you're not just bewildered by the many options in front of you.
So when a new member comes into the space and they want to use a tool for the first time or an old tool in a new way that they haven't used it before, they just hit a button that we have on the wall that says, I need help.
- [Robotic Voice] A human will be with you in a moment.
- And that has our AI here contact us and tell us that someone needs help and where they are.
And then we go out and we find out what process they're gonna go through.
And that lets us teach someone how to rip a board or crosscut a board or bend a piece of steel or make a simple weld or any of these other operations as a one-off training experience where they can learn how to do that one thing in isolation very quickly and safely, so that they can get on with their project, rather than trying to eat the entire elephant at once, we want to take it one little bite at a time.
One of the ways that we differ from a lot of other makerspaces is that we have services that we provide beyond simply access to the tools.
So if we have a digital tool like a laser cutter or a CNC machine, it's very common for us to have that as a service only tool where an operator is going to take your design and turn it into a finished object for you, using materials that we keep on hand.
I really like to think that that's what a makerspace is for, is we're taking that hot, fresh idea that you just, you just had right now, you and a friend are talking about something amazing that you'd like to see birthed into the world and you realize that you can just go do that right now and strike while the iron's hot and make the thing while the monkey on your back is still actively screaming, rather than six months or a year from now when you finally get your ducks in a row and have all the tools lined up.
So, that to me is where makerspace births ideas.
It's an engine that just makes reality come out of your head more easily because you've removed the obstacles to your creativity.
It's why I do this.
(upbeat music) - I am a calligrapher, engraver and watercolor artist.
So calligraphy, like the short meaning is like, the art of beautiful handwriting, but it's actually like a visual art that applies the execution of strokes using, it could be ink and nib, it could be watercolor, it could be a brush, it could be a brush pen.
So combining these strokes in order to achieve a beautiful form of lettering.
It doesn't care about like your penmanship.
You could have a really bad penmanship or you could have the best penmanship in the world and it would not affect your calligraphy.
There's only like two basic principles in calligraphy.
As long as all your upward strokes are thin and all your downward strokes are thick, then you achieve like the beautiful lettering of calligraphy.
To create the thin and thick lines, there's a application and the release of pressure to make the thick lines, that's all downward strokes, you apply pressure and your nibs actually have two times that split.
So when you apply that pressure and when you bring that nib down and you create a thick stroke, on the other hand, when you bring that nib upward, then you don't apply any pressure at all.
Then that's how you create the thin lines.
It's positioning versus the application of pressure.
There's four basic strokes that I usually teach my students in a class.
The thin stroke or the upward stroke, which is also called the entrance or the exit stroke.
And then there's oval, there's a compound curve, or it's like the wave.
It's a combination of thin and thick strokes altogether.
And there's also the downward stroke, which is all thick line.
So if you master the application and the release of pressure within all those four strokes and then you combine those strokes to build the letters, then you could be the next big calligrapher out there.
So my business is called the Tawny Canvas, and basically I offer all things calligraphy, engraving, watercolor.
My target clients are brides and grooms, which, the wedding industry loves calligraphy cause it's really pretty on envelopes and invitations.
I also hold like calligraphy workshops for like bridal showers and birthdays.
Then I also do envelope addressing, place cards, wedding signs.
For engraving, I usually have bigger clients like Nordstrom and Macy's.
So they have like special sales, like Mother's Day Event or Christmas or Valentine's and they usually place me in the perfume section cause it's glass and so when people buy anything it's like complimentary, who wouldn't want a perfume with their name on it?
Looking sparkly gold or silver like that.
So it's like doing full calligraphy.
First of all, you sketch out whatever you wanna write, like some, mostly something in cursive.
So I would like sketch that out using like a white pencil that I could just rub off.
I engrave it, like with a monoline, like just trace my draft and then I go over it again, making sure that all of my downward strokes should be thick.
You have to like, be patient and go over it over and over again until you achieve the certain thickness of the stroke.
I love calligraphy because it allows me to enjoy the present.
Nowadays everything's like rush, rush, rush, everybody's busy, go, go, go.
But then in calligraphy it's important to like slow down.
Like it allows me to breathe.
It allows me to like ride strokes and not be in a hurry.
So it allows me to be more present and I like that because that's rare for me, like as a person.
So it relaxes me.
It's kind of like meditation, except that you're doing something.
So that's the best part about calligraphy.
It's like therapy to me.
One thing I like besides the process of creating the art, is getting to share this passion with other people.
I have the privilege of doing that, sharing this crazy passion of mine towards others.
I like that when they leave, they get to leave with a hobby and I hope one day, many years from now, they get to be as inspired as I am and I hope calligraphy becomes a therapy for them too.
So it's nice to share that my love of calligraphy to them hopefully like to be a part of their artistic journey.
It's cliche but like love inspires me because I wanna make this for someone.
It's always not for myself, but it's actually giving something beautiful and something personal to somebody else.
So that's why I do what I do.
Like seeing the brides face with their invitation, it just makes me happy too.
So it's like, making this world a better place with like one artwork at a time.
- [Matt] Now are you taking that flash off with that wheel also?
- [Dave] Yep.
- So we're back here today at Hammerspace and I'm standing here with Dave and you've got quite a bit of stuff laid out for us here.
What sort of project are we working on?
- Well today, you're in luck.
We're gonna be doing a really fun project where we're gonna be casting some metal.
Now metal casting is generally fraught with all sorts of peril, special equipment, super high temperatures.
- Yeah, we're not wearing respirators here.
- No, it's nothing like that.
It's pretty tame for metal casting.
I think metal casting is really like the foundational element of all of the metal arts because before we could do anything else, we needed to cast some metal into a single piece so we can use it for, - I have to make a tool so I can make my other tool that I need.
- Exactly.
So from that first campfire where some shiny metal coagulated under the campfire, humanity's been casting metal.
Now the bronze age is named for bronze, which is an alloy of copper and tin.
- [Matt] Okay.
- And it's really hard to melt bronze in your house.
Like you need about 2,000 degrees to melt bronze and that's hard to achieve in normal circumstances and without special equipment.
- And air conditioning space and all that.
- Exactly.
So today we're gonna use anti bronze, kind of the opposite of bronze if you will.
- Okay.
- It's pewter.
- All right.
- Now pewter's a different alloy with exactly the same stuff in it.
It's also made out of copper and tin, just in opposite ratios.
- So far more tin than copper?
- Almost all tin with a little tiny copper as opposed to being almost entirely copper with a little bit of tin.
Paper burns at about 451 degrees Fahrenheit ish.
And MDF or medium density fiberboard, is considerably thicker than paper.
So this is just the same stuff that paper's made out of.
This is sawdust reconstituted into a solid piece of material and this is durable enough to withstand molten pewter being poured onto it.
So today we've made something called a billet mold.
This is an entirely digital process.
We drew these on our computers, over in the computer lab, using a vector drawing program.
So just graphic design software, and we drew some logos and laid them out and then took that design down to the laser shop.
Over in the laser shop we used some CO2 lasers to cut and etch these into the final shape.
- So that was all one process and one machine?
- Yes, one machine did the etching and the cutting all at once.
This helps us with registration.
Now this part of it, we have sort of this channel that comes down to our coin shape at the bottom.
And this is replacing structures in a regular casting process known as the button, which is kind of the fill spout of our mold and the sprews, which are straw like appendages that go to different parts of your part to help deliver metal to those parts and to evacuate air from the part.
- [Matt] Well, what's our first step here?
- Well our first step is to take some of these shapes and assemble them together.
So if you'd like to pick out something, I've got a couple here that I've already pre-built.
- Let's go.
We'll do my logo and your logo there.
- [Dave] All right.
So go ahead and stack those up.
- [Matt] Okay.
- I like to make sure that it's nice and flat on a table or surface when I start.
And we just wanna put some pressure around the perimeter so it doesn't leak.
And then I usually use these to get it a little stability there.
Make a little stand out of our clamps, and then we'll want some safety glasses because if we should splash some pewter, it should just roll off of us, but not our eyes.
- [Matt] That's fair.
- So then we'll take some of our clean pewter and we're gonna pour it into our mold.
We want to kind of pour it all at once so that we fill all the way up to the top and a little over spill is just fine.
- [Matt] Now how long will that need to sit in the mold until it's ready to come out?
- [Dave] Only a minute or two.
- Okay.
Because it's not, there's not a whole lot of mass there.
- It's pretty thin.
It's gonna be hot for probably about three or four minutes and then it should be ready to demold at that point.
- Okay.
Okay, so it's been, we've had that in there for what, three or four minutes, give or take?
- [Dave] Yeah, more or less, three or four minutes and now we can see what we've got.
There we go, it's cool.
Now at this point it's gonna be hard to see the details because we're gonna have all sorts of surface discoloration from the casting process, but, - [Matt] That didn't turn out bad at all.
- And that's our first try on this mold.
Now typically your second casting on a mold, looks a little better than your first one because MDF is full of glue and formaldehyde and all kinds of other stuff that boils just a little bit at these temperatures so it'll mess up our surface finish.
- [Matt] So you kind of like caramelized the mold?
- The surface.
Right, right and now the second casting in it, it's like going into a carbon mold now, it's gonna do much better on a second casting.
And then I've got some shears here that we can separate our excess material and so it wasn't wasted, even though we poured all that extra material, it just goes right back into the caster and gets recycled.
- Perfect.
- So now that we've cleaned up the edges of our coins a little bit, got rid of the remnants of the sprew and, - We're just talking about the little, - Just that little bit that's left there.
I cleaned that off of this one and it's all ready to go.
But they look a bit humble when they come out of the mold because we just have the raw surface of the metal there.
So I have a secret that I use for patinaing these coins.
It's a dry erase marker because we want to use something that's really permanent.
- [Matt] Perfect.
- And then we're gonna wipe it off with some steel wool.
Now this is not ordinary kitchen steel wool.
This is some for fine finishing.
It's like a quadruple OT steel wool.
So the type with the four zeros on it, this is really, really fine.
- [Matt] Right.
- [Dave] So this isn't gonna scratch our coin up, it's just gonna shine it up and give it a little luster.
- [Matt] So you said we can reuse these molds.
We've got a couple more molds to use and we've still got some metal hot, what do you say we make a couple more?
- [Dave] Let's make a pile of coins.
- [Matt] Let's do it.
So that didn't take very long at all.
We got a pile of coins going.
- Yeah, I feel like we will just open our own mint right here and start minting our own currency.
(upbeat music) - I am a flower preservation artist and that means that I work with fresh flowers and I preserve them to keeping their original colors and textures and things like that.
And then create art from those flowers after they have already dried so that they can be enjoyed for many, many years to come.
Multiple members of my family have been in the flower industry.
So my aunt has been a florist for my entire life.
Both my mom and grandmother have also worked in the florist industry.
So I've just grown up around flower culture a lot and always been drawn to that.
And so I've always had a really big passion for flowers and a really big passion for art.
And so once I began doing this, I really just felt like those two passions collided.
And I began preserving specifically wedding bouquets, after I was married about five years ago.
And so I wanted to preserve my own wedding bouquet.
I loved my wedding flowers, my aunt made them and I wanted to keep them.
And so like right before we were getting on our honeymoon flight, I was like getting down all my big books and shoving flowers in between the pages and hoping that they would be fine when I came back a week later and it was, I think maybe the first time where I was like, I think this is like the niche I wanna be in.
99% of my clients are all brides, or newly married couples.
And they book with me several months up to a year out in advance.
And I offer my clients two different kinds of design styles.
The first is traditional, which means I'm designing their bouquet in a more bouquet like shape.
So that's a little bit more traditional in the fact that the design that they are getting from me is gonna look more like their bouquet did on their wedding day in the bouquet shape.
A modern design style is where I play off of the individual shapes of the flowers themselves.
And there's a lot more air left in between them.
And I kind of look at the individual shape of each flower before placing it down and let them kind of play with each other and move throughout the piece.
So it focuses more on the beauty of each individual flower and the textures and things there.
Whereas the traditional design is more, it gives you the feeling of an overall bouquet.
They have to have their flowers to my studio within four days following the wedding or event.
And so I have them shipped to me from all over the country and then also dropped off locally, just within a few days following their wedding.
And that really is so important because if they wait, they're too far gone to begin preservation.
Each flower has its own recipe for preserving and retaining its color and texture.
And so I just follow a variety of different methods using a micro press, a wooden press, some books, to press each flour individually.
And then once they have finished their pressing process, which can take anywhere from two weeks for a smaller flower to almost two months for a larger flower like a rose or something like that, based on each individual's flowers, unique qualities, I've kind of figured out how it responds best to pressing and dehydrating to preserve its colors.
And so once I have finished pressing and preserving all of the flowers, then I begin laying out their design, playing with it.
And I normally take a picture of the bouquet when I first get it in.
And so then if I need to, I'll look back at that and kind of see, okay, this was the feeling of their bouquet, especially if they choose a traditional design.
I'll look back at that photo, kind of see the shape of their bouquet, and then design it from there to kind of match the, the same shape that it had then.
And also just play with the flowers and see how they fill the frame.
Because I have probably eight to 10 different framing designs, whether it's an 8x10, 11x14, 16x20, or I have some more unique design options that are made out of like circles and triangles and things like that.
And then I'll begin gluing and arranging the flowers in their design that I've created.
Once that process is done, then they go on to framing, which is also a big part of the process, keeping out dust particles, pet hair, just anything that could get inside the frame because I'm creating family heirlooms to last a lifetime.
And once that's complete, then I photograph every piece, email them a finished photo and pack it either for shipping or let them know it's ready for local pickup.
So when I began, I don't think I realized how much meaning flowers held.
I always loved flowers because I just, I personally, I enjoyed them, but I don't think I realized how much value they hold for other people.
And so I've really began to understand that after I've been doing this work for several years now.
That when I am, the flowers I'm preserving, like those were the flowers someone held on their wedding day.
And that's something that they like keep back and look and remember that day for so many years to come or when it is a memorial flower.
That was a really hard day, but it's a little, just momentum that they could have and keep and remember that really beautiful life in a really beautiful way.
That's what I really enjoy about my work, is preserving these, not only flowers, but these memories for people as well.
- So I'd like to thank Dave, everyone here at KC Hammerspace and all of our other makers for sharing their time with us today.
That wraps up our show for this week, but I hope all of our makers have inspired you to unlock your creative spirit.
Thank you for watching and we hope you'll join us here next time, to see what we'll be making.
More information is available on social media or online at kmos.org.
This program was made possible by contributions to your PBS station from viewers like you.
Thank you.
(upbeat music)
Hammerspace Community Workshop
Video has Closed Captions
Hammerspace Community Workshop – Kansas City, MO (6m 21s)
Video has Closed Captions
Hannah Klein Design – Pressed Flowers – Neosho, MO (5m 35s)
Video has Closed Captions
How-to Cast Pewter @ Hammerspace Community Workshop (6m 50s)
Providing Support for PBS.org
Learn Moreabout PBS online sponsorshipMaking is a local public television program presented by KMOS